An Explanation of Hook Latches: What They Are and Their Functionality
- Bundit Suriyaburaphakul
- May 28, 2023
- 3 min read
Hook latches play a crucial role in ensuring the safety and security of lifting operations. These small but important components are designed to enhance the functionality and reliability of hooks used in various rigging applications. In this article, we will explore the purpose and functionality of hook latches, their types, and the benefits they offer in terms of safety and convenience.
Hook latches, also known as safety latches or safety catches, are mechanisms attached to the throat of a hook. Their primary function is to prevent the accidental disengagement of the load from the hook during lifting operations. By providing an additional barrier, hook latches help secure the load and minimize the risk of slippage or detachment, thereby ensuring the safety of both the workers and the load being lifted.
There are different types of hook latches available, each designed to suit specific applications and lifting requirements. One common type is the spring-loaded latch, which utilizes a spring mechanism to keep the latch in a closed position. This type of latch automatically locks when the load is engaged, providing continuous security throughout the lifting process. Another type is the positive locking latch, which requires manual engagement and disengagement, offering additional control and security.
The functionality of hook latches is simple yet effective. When properly engaged, the latch covers the opening of the hook, preventing the load from accidentally sliding off. This adds an extra layer of protection and ensures that the load remains securely attached to the hook until intentionally released.
The benefits of hook latches are numerous. Firstly, they enhance safety by minimizing the risk of load disengagement and potential accidents. The latch acts as a fail-safe mechanism, reducing the likelihood of unintended load release, which could result in property damage, injury, or even loss of life.
Secondly, hook latches provide convenience and peace of mind for operators. By securely holding the load in place, they eliminate the need for constant manual monitoring and gripping, allowing operators to focus on other critical aspects of the lifting operation. This improves efficiency and reduces operator fatigue.
Lastly, hook latches contribute to the longevity and durability of the lifting equipment. By preventing the load from rubbing against the throat of the hook, they help minimize wear and tear, extending the lifespan of both the hook and the latch itself. This translates to cost savings in terms of maintenance and replacement.
In conclusion, hook latches are vital components in lifting operations, providing an added layer of safety, convenience, and equipment protection. Understanding their purpose and functionality is essential for ensuring proper usage and adherence to safety guidelines. By incorporating hook latches into rigging practices, operators can enhance safety, improve efficiency, and protect their valuable assets.
The throat opening of a hook can be closed with a mechanical device known as a latch, as defined by ASME B30.10. The main purpose of using a latch is to reduce the possibility of the rigging becoming detached from the hook, especially in slack conditions. However, the use of a hook with a latch does not entirely eliminate the risk of accidental detachment of a slack sling or a load from the hook.
It is important to note that hook latches are not anti-fouling devices during load handling or rigging and are intended to aid in the retention of loose slings under slack rigging conditions only. Also, a latch is not designed or rated to carry a significant load, as stated by ASME B30.10.
Crosby recommends using a latch in most cases, and compliance with this recommendation is often required by standards and safety regulations, such as OSHA. Thus, using latches is considered a best practice. Crosby advises consulting and adhering to the guidance provided by ASME, OSHA, and other safety administrations.
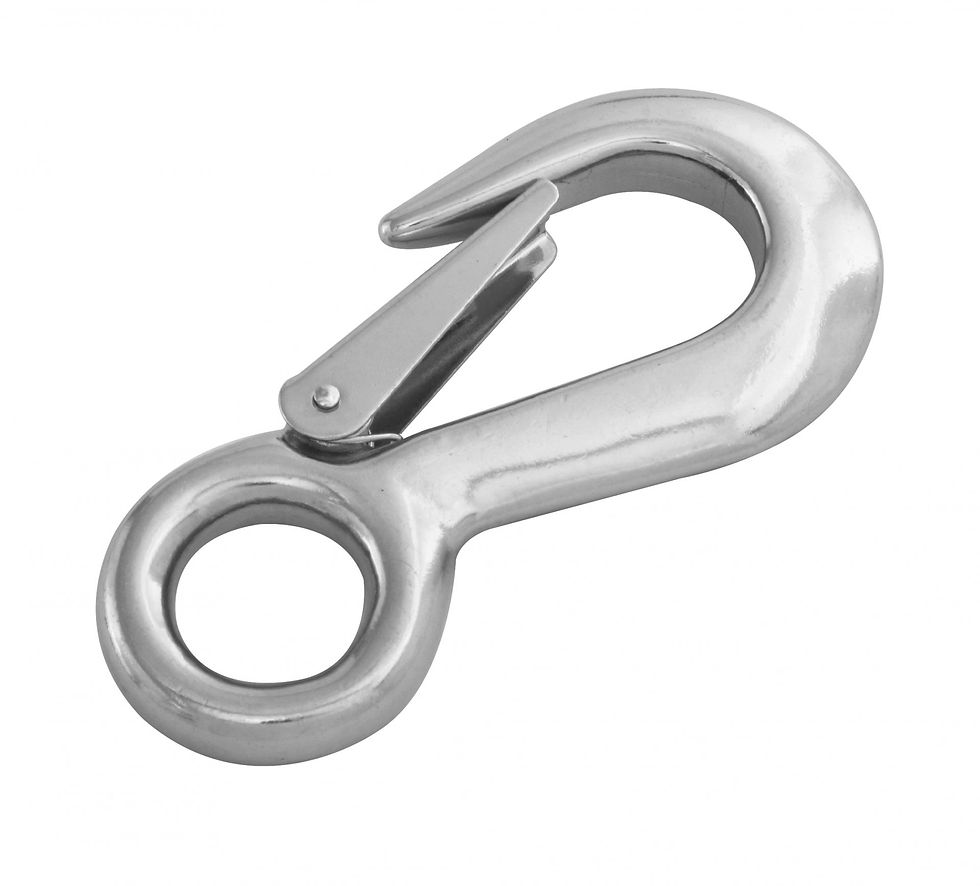
Comments